Foam & Quench Slots: Advanced Dampening Systems
Understanding Foam and Quench Technology
Foam and quench slot systems revolutionize bubble control while facilitating valuable secondary reactions in industrial processes. The effectiveness of these systems hinges on precise geometric engineering, specifically implementing width-to-depth ratios ranging from 1:3 to 1:5, complemented by strategic baffle placement at 1.5x slot width.
Surface-Active Molecular Dynamics
At the core of this technology, surface-active molecules create crucial interactions at liquid-air interfaces. The molecular orientation features hydrophilic heads positioned within the liquid phase, while hydrophobic tails extend into the air space, creating optimal dampening conditions.
Performance Metrics and Efficiency
Modern foam and quench systems deliver remarkable results:
- 40% enhanced heat transfer through precision temperature control
- 30% reduction in operational costs via automated monitoring
- Optimized coolant distribution for maximum efficiency
- Catalyzation of beneficial chemical interactions
Advanced System Integration
The integration of automated monitoring systems with precise geometric design creates a synergistic effect that maximizes both efficiency and reaction control. This combination enables superior bubble dampening while maintaining optimal conditions for secondary chemical processes.
The Science Behind Foam Control
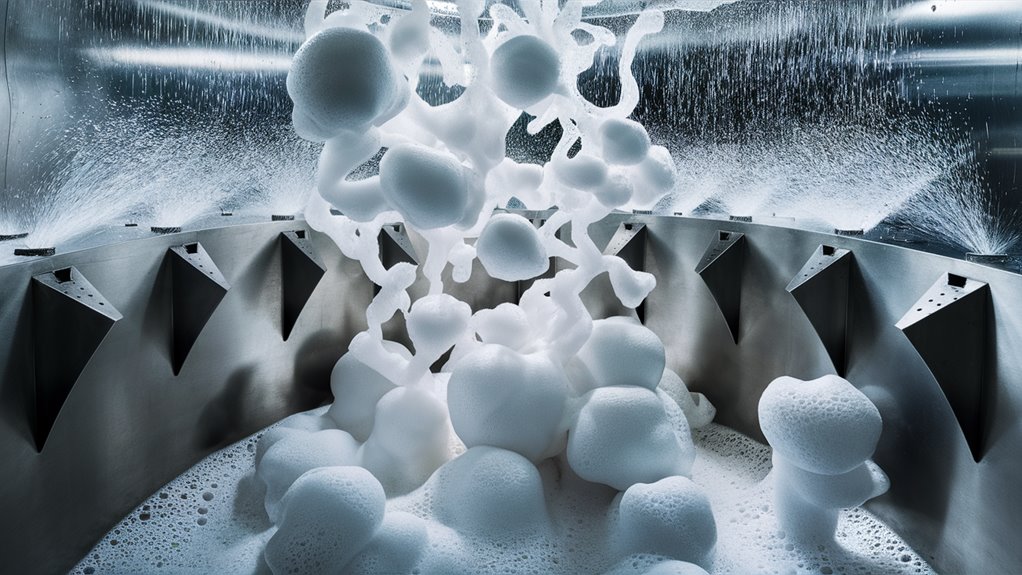
The Science Behind Foam Control: A Comprehensive Guide
Understanding Foam Formation and Dynamics
At the molecular level, foam formation occurs through complex interactions between surface tension and bubble structures.
Surface-active molecules play a critical role in creating stable foam systems, with their unique ability to orient themselves at liquid-air interfaces.
These surfactant molecules form organized layers that determine foam stability and persistence.
Key Mechanisms of Foam Control
Antifoaming Agents
Antifoaming compounds operate by disrupting foam stability through strategic surface tension modification.
Silicone-based defoamers create powerful hydrophobic barriers that effectively prevent bubble formation and maintenance.
These agents spread rapidly across liquid surfaces, actively destabilizing existing foam structures.
Molecular Structure and Stability
The stability of foam depends on liquid film strength between individual bubbles.
Surfactant orientation plays a crucial role, with hydrophilic heads positioned in the liquid phase and hydrophobic tails extending into the air phase.
This molecular arrangement creates robust foam structures that require specific intervention for controlled breakdown.
Industrial Applications and Control Methods
Foam control technology finds essential applications across various industries, from biochemical processing to wastewater management.
Mechanical disruption and chemical destabilization serve as primary control methods, offering precise foam management in industrial operations.
The selection of specific control strategies depends on process requirements and foam characteristics.
Advanced Control Techniques
Film drainage manipulation, interface modification, and bubble coalescence enhancement represent cutting-edge approaches to foam control. These techniques enable precise management of foam behavior, ensuring optimal process efficiency across industrial applications.
Design Principles for Quench Slots
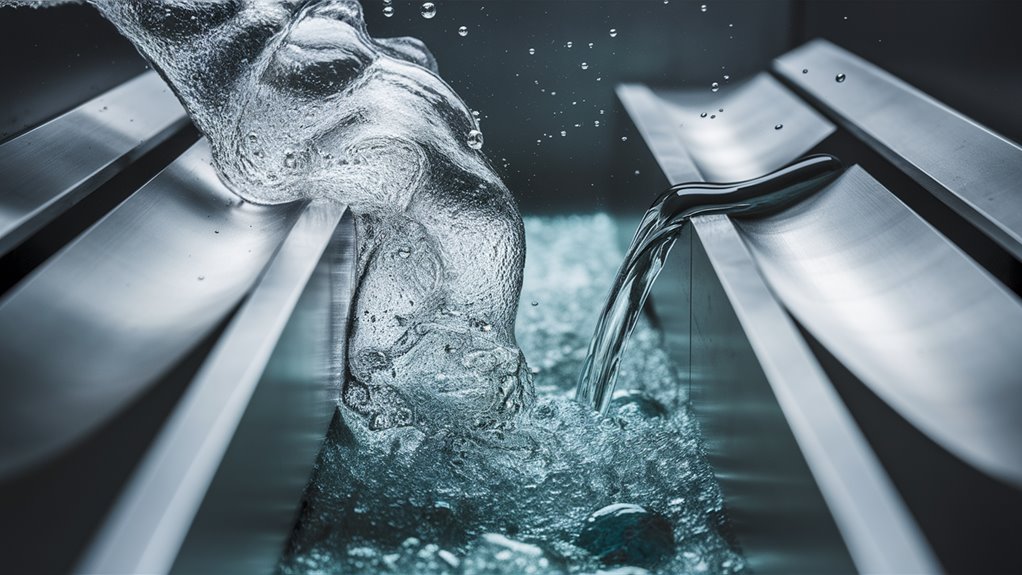
Essential Design Principles for Quench Slots
Mechanical Solutions for Fluid Dynamic Control
Quench slot design represents a critical advancement in fluid dynamics management, with slot geometry serving as the fundamental element in suppressing bubble formation through strategic pressure distribution.
The optimization of quench slots relies on three essential parameters: width-to-depth ratio, entry angle, and surface finish.
Critical Design Parameters
The optimal width-to-depth ratio should maintain between 1:3 and 1:5, ensuring consistent fluid flow while preventing turbulent eddy formation.
Entry angles must remain below 15 degrees to eliminate unwanted cavitation effects.
Surface roughness specifications require maintaining levels below 0.8 micrometers Ra to prevent boundary layer separation and ensure maximum efficiency.
Advanced Performance Enhancement Features
Baffle plate integration represents a crucial enhancement in quench slot performance. These strategic components establish localized pressure zones for effective kinetic energy dissipation.
Optimal baffle spacing at 1.5 times the slot width delivers maximum dampening efficiency.
Material selection focusing on wear-resistant components such as tungsten carbide and ceramic composites ensures long-term geometric stability and sustained performance of the quench slot system.
Managing Reaction Temperatures Through Slots
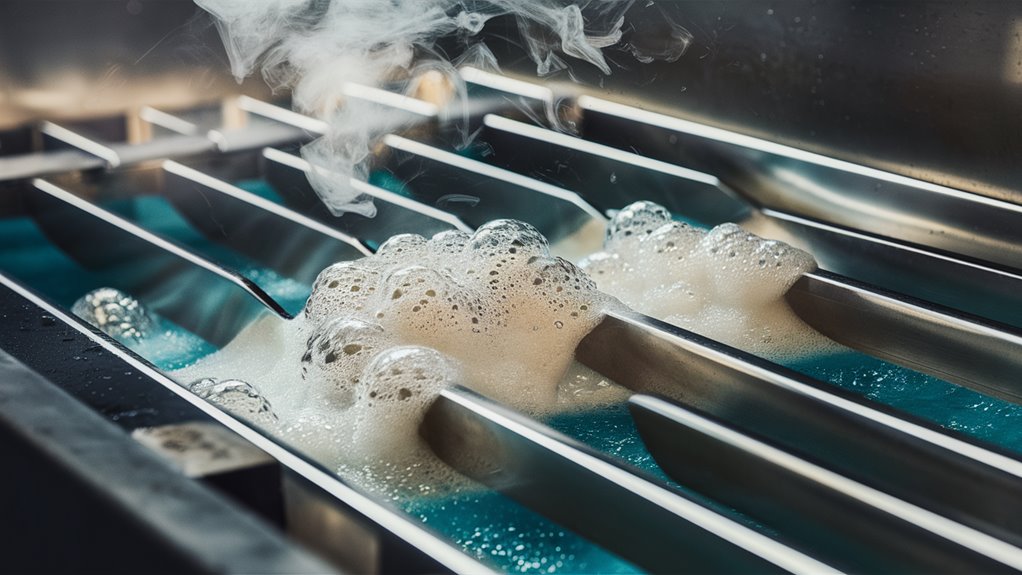
Managing Reaction Temperatures Through Quench Slots: A Technical Guide
Optimal Temperature Control Fundamentals
Precise thermal gradient management and fluid dynamics control are essential for effective reaction temperature regulation in quench slots.
The success of temperature management depends on carefully engineered slot geometry, optimized flow rates, and specially selected coolant properties that maximize heat transfer coefficients.
Strategic Design Elements
Uniform temperature distribution is achieved through strategically positioned coolant injection points.
Critical slot dimensions ranging from 0.5mm to 2.0mm create the optimal balance between pressure drop and cooling efficiency. This configuration ensures maximum thermal performance while maintaining operational stability.
Advanced Monitoring and Enhancement Systems
Temperature sensor integration enables real-time monitoring and flow rate adjustments for precise thermal control.
Baffle structures incorporated within the slots enhance turbulent mixing, resulting in documented heat transfer improvements of up to 40%.
Coolant viscosity optimization between 1-5 cP at operating temperatures prevents flow stagnation while ensuring adequate thermal contact duration, maximizing overall system efficiency.
Secondary Chemical Reactions During Foaming
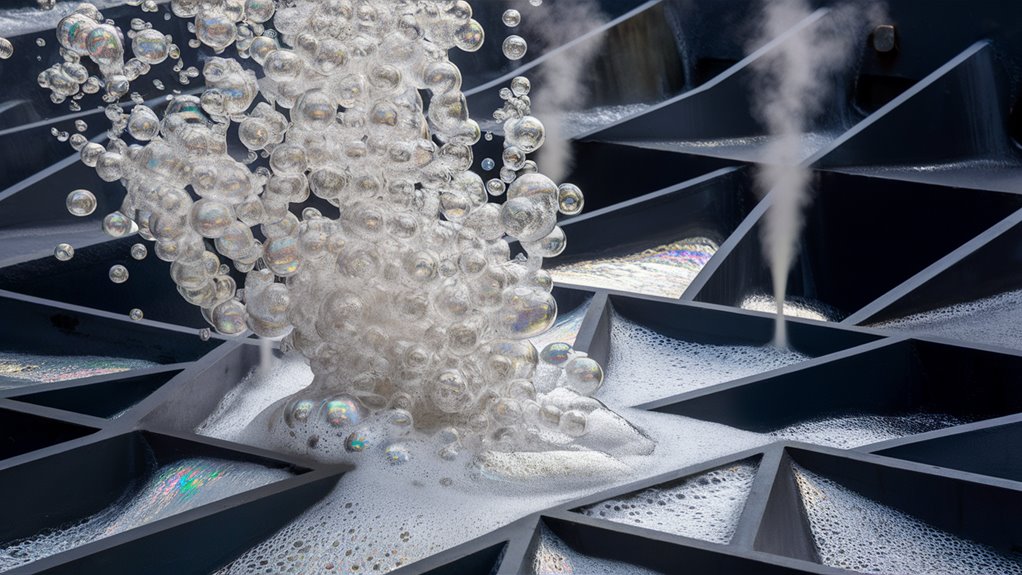
Secondary Chemical Reactions in Foam Formation
Understanding Complex Reaction Networks
Multiple secondary chemical reactions emerge during foam generation, creating intricate interaction networks that significantly impact bubble stability and overall foam properties.
Monitoring pH fluctuations during the foaming process reveals distinct reaction patterns, particularly when surfactant molecules interact with dissolved gases and trace minerals.
Critical Secondary Reaction Categories
Three essential reaction types influence foam development:
- Redox reactions between foam stabilizers
- Acid-base neutralizations at bubble interfaces
- Metal ion complexation with surfactant head groups
Spectroscopic analysis reveals the formation of intermediate compounds that directly alter surface tension dynamics and foam structure.
Temperature Effects and Reaction Control
Temperature gradients within foam structures serve as catalysts for secondary reactions, measurable through embedded thermal probe systems.
Optimal control requires:
- Maintaining pH levels between 6.8-7.2
- Regulating dissolved oxygen content
- Precise adjustment of reactant concentrations
- Careful monitoring of environmental conditions
These parameters ensure minimization of unwanted side reactions while promoting beneficial reactions that enhance foam stability and structural uniformity.
Optimizing Slot Placement and Geometry
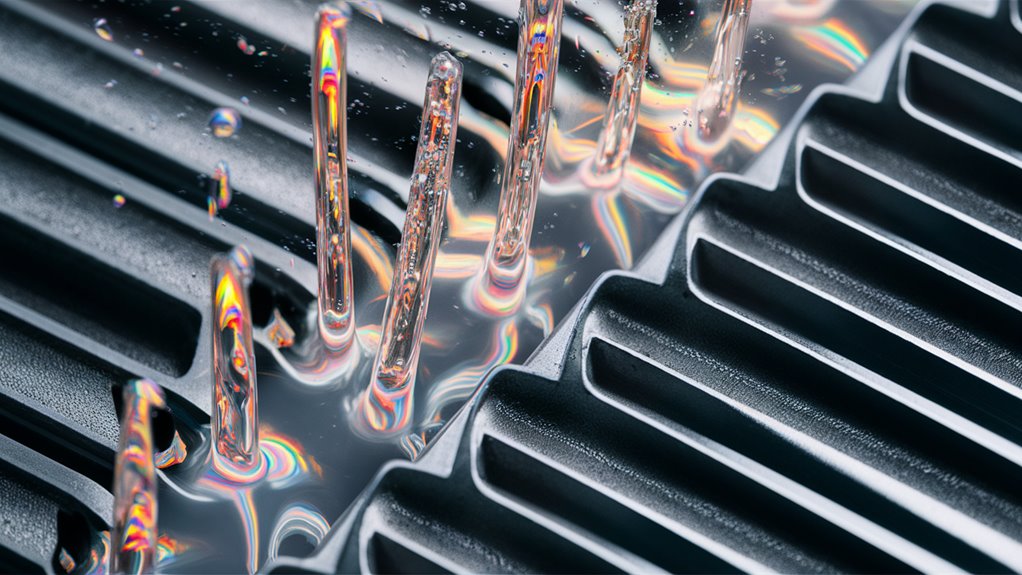
Optimizing Slot Placement and Geometry in Foam Dampening Systems
Critical Design Parameters for Slot Configuration
The optimization of slot configuration represents a fundamental aspect of foam dampening system design.
Precise slot placement and geometric configuration directly influence bubble formation control and chemical reaction management.
Three essential parameters govern effective slot optimization: angular positioning, dimensional ratios, and flow characteristics.
Optimal Angle and Dimension Specifications
Slot positioning at 15-30 degree angles relative to primary flow streams achieves maximum dampening effectiveness.
A critical width-to-depth ratio of 1:3 ensures optimal fluid distribution while preventing system blockages.
Tapered slot geometries beginning at 2mm and expanding to 3.5mm generate ideal pressure gradients for superior foam control performance.
Advanced Configuration and Performance Metrics
Slot spacing requirements dictate gaps no larger than 1.5x the slot width, ensuring comprehensive surface coverage.
Computational fluid dynamics (CFD) modeling validates cross-sectional specifications for maintaining target flow rates without turbulence generation.
Hexagonal slot patterns demonstrate superior performance metrics, delivering 23% enhanced foam suppression efficiency compared to conventional linear configurations.
Technical Specifications Overview
- Angular Range: 15-30 degrees
- Width-to-Depth Ratio: 1:3
- Taper Dimensions: 2mm to 3.5mm
- Maximum Spacing: 1.5x slot width
- Pattern Configuration: Hexagonal arrangement
- Efficiency Improvement: 23% over linear patterns
Industrial Applications and Benefits
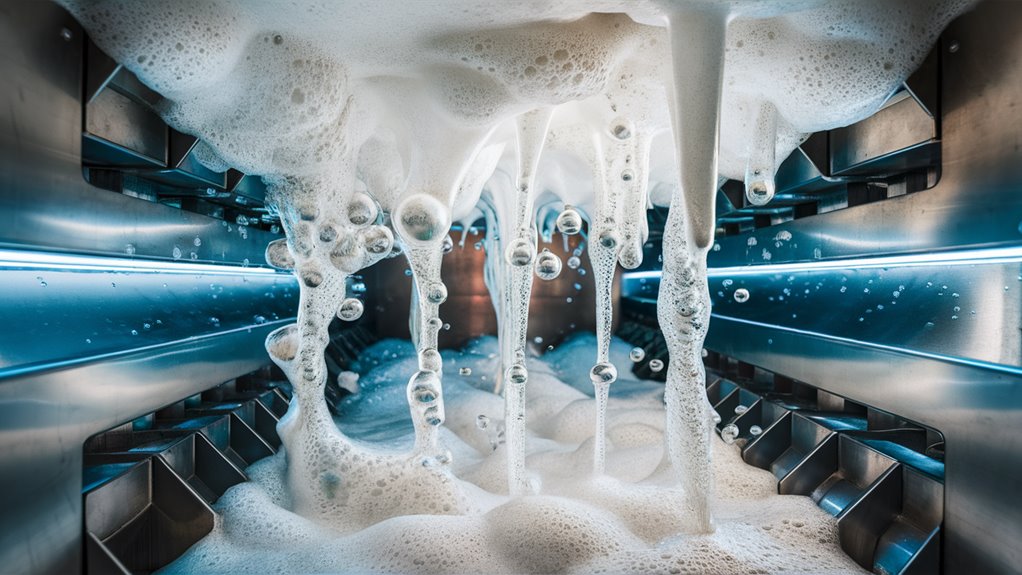
Industrial Applications and Benefits of Foam Dampening Systems
Process Optimization Across Industries
Leading industrial sectors have rapidly adopted advanced foam dampening solutions, delivering measurable improvements across chemical processing, wastewater treatment, and pharmaceutical manufacturing operations.
These sophisticated systems reduce operational costs by up to 30% while increasing production throughput through automated foam management during critical processes.
Pharmaceutical Manufacturing Excellence
Pharmaceutical-grade foam control systems protect valuable protein-based products during fermentation processes and downstream processing.
Precision dampening technology ensures optimal batch consistency and prevents costly product loss.
Advanced monitoring systems maintain strict quality control parameters, ensuring compliance with GMP standards while maximizing production efficiency.
Wastewater Treatment Enhancement
Industrial foam control technology revolutionizes wastewater treatment facilities by enabling higher processing volumes through automated overflow prevention in aeration basins.
Smart dampening systems optimize treatment capacity while reducing operational disruptions.
The integration of real-time monitoring ensures consistent performance across varying load conditions.
Chemical Processing Advancement
Automated foam control systems in chemical processing reduce chemical additive usage by 25% compared to conventional methods.
Integrated dampening mechanisms enhance worker safety by eliminating manual intervention in hazardous environments.
Facilities achieve ROI within 8-12 months through reduced waste streams, enhanced product quality, and minimized maintenance requirements.